PGF/YDL
Can filler and seamer
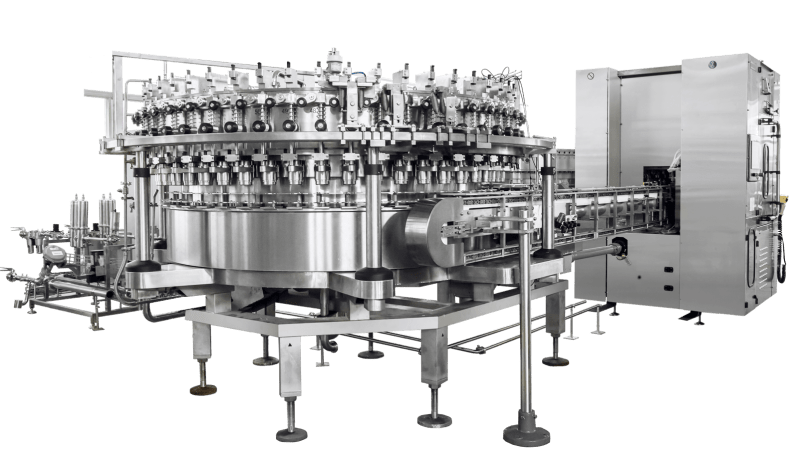
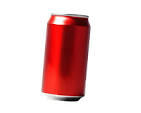
Capacity:
Up to 90.000 CPH
Carbonated and Non-carbonated Drinks
Brief Introduction:
- The short tube filler or volumetric can filler in hygienic design is used to fill beer or carbonated soft drinks in aluminum cans.
- Can filler and seamer are integrated and filler is blocked with a seamer and is driven by a frequency-controlled motor.
- The cans are supplied to the filler in handling parts, designed for quick changeover, and made from high wear-resistant plastic material.
- Both cold fill and warm fill up to 15C are possible.
- The fill height is either controlled by vent tubes or volumetric control to ensure high fill level accuracy.
- All parameters can be easily adjusted on the HMI.
- The filler is equipped with oxygen measurement and fully automatic CIP and COP process.
- All parts of the filler are designed for easy cleaning and sterilization.
MACHINE BENEFITS | |||
1. Hygienic design with automated CIP and COP. | |||
2. Circular type ring bowl in sanitary design without dead spaces. | |||
3. Motorized height adjustment of filler bowl to adapt the filler to different SKUs. | |||
4. Automatic filling speed control according to infeed/discharge product flow. The infeed is automatically stopped if the flow of empty cans is interrupted. Filling speed and can counter are displayed on the HMI. | |||
5. Reliable plastic infeed star wheels for quick changeover and fast release. | |||
6. Coupling joint connection between filler and the seamer to ensure synchronization. | |||
7. Dissolved oxygen measurement and control. | |||
8. Hygienic central supply pipe to avoid cross-contamination between product (CO2/CIP) and operation gas, with no fluid or gas accumulation for easy cleaning. | |||
9. Stable operation, filling volume is pre-set at the HMI for high filling accuracy. Minimized product loss. | |||
10. Microbiological safe guiding parts with self-contained star wheels, open guiding curves and streamlined support parts to eliminate dead spaces, ensuring complete cleaning and sterilization of all outside surfaces. | |||
11. Glass observation window in the product supply pipe. | |||
12. Auto CIP dummy cups as an option. | |||
13. Microbiological safe guiding parts with self-contained star wheels, open guiding curves and streamlined support parts to eliminate dead spaces to ensure complete cleaning and sterilization of all outside surfaces. | |||
14. Glass observation window in the product supply pipe. | |||
15. Auto CIP dummy cups as an option.
———- |
Production capacity of can filler and seamer:
Ringbowl diameter | Number of valves | Capacity per hour | |
1,600 | 32 | 6.000 to 15.000 | |
2,000 | 40 or 50 | 15.000 to 36.000 | |
2,400 | 60 | 27.000 to 40.000 | |
2,166 | 76 | 32.000 to 50.000 | |
2,622 | 92 | 43.000 to 60.000 | |
3,078 | 108 | 51.000 to 72.000 | |
3,648 | 128 | 60.000 to 90.000 | |
4,104 | 144 | 90.000 to 120.000 |
————————————————– FILLING TECHNOLOGY |
|||
1. PGF: Mechanical filler with vent tubes and cam control. | |||
2. YDL: Volumetric filler with measuring cylinder for filling volume control with deviation within ±1ml. |
* Add notice about your Privacy Policy here
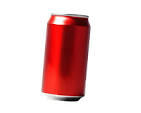
Capacity:
Up to 90.000 cph
Carbonated and Non-carbonated Drinks
Brief Introduction:
- The short tube filler or volumetric can filler in hygienic design is used to fill beer or carbonated soft drinks in aluminum cans.
- Can filler and seamer are integrated and filler is blocked with a seamer and is driven by a frequency-controlled motor.
- The cans are supplied to the filler in handling parts, designed for quick changeover, and made from high wear-resistant plastic material.
- Both cold fill and warm fill up to 15C are possible.
- The fill height is either controlled by vent tubes or volumetric control to ensure high fill level accuracy.
- All parameters can be easily adjusted on the HMI.
- The filler is equipped with oxygen measurement and fully automatic CIP and COP process.
- All parts of the filler are designed for easy cleaning and sterilization.
MACHINE BENEFITS | |||
1. Hygienic design with automated CIP and COP. | |||
2. Circular type ring bowl in sanitary design without dead spaces. | |||
3. Motorized height adjustment of filler bowl to adapt the filler to different SKUs. | |||
4. Automatic filling speed control according to infeed/discharge product flow. The infeed is automatically stopped if the flow of empty cans is interrupted. Filling speed and can counter are displayed on the HMI. | |||
5. Reliable plastic infeed star wheels for quick changeover and fast release. | |||
6. Coupling joint connection between filler and the seamer to ensure synchronization. | |||
7. Dissolved oxygen measurement and control. | |||
8. Hygienic central supply pipe to avoid cross-contamination between product (CO2/CIP) and operation gas, with no fluid or gas accumulation for easy cleaning. | |||
9. Stable operation, filling volume is pre-set at the HMI for high filling accuracy. Minimized product loss. | |||
10. Microbiological safe guiding parts with self-contained star wheels, open guiding curves and streamlined support parts to eliminate dead spaces, ensuring complete cleaning and sterilization of all outside surfaces. | |||
11. Glass observation window in the product supply pipe. | |||
12. Auto CIP dummy cups as an option. | |||
13. Microbiological safe guiding parts with self-contained star wheels, open guiding curves and streamlined support parts to eliminate dead spaces to ensure complete cleaning and sterilization of all outside surfaces. | |||
14. Glass observation window in the product supply pipe. | |||
15. Auto CIP dummy cups as an option. |
Production capacity of can filler and seamer:
PRODUCTION CAPACITY | |||
Ringbowl diameter | Number of valves | Capacity per hour | |
1,600 | 32 | 6.000 to 15.000 | |
2,000 | 40 or 50 | 15.000 to 36.000 | |
2,400 | 60 | 27.000 to 40.000 | |
2,166 | 76 | 32.000 to 50.000 | |
2,622 | 92 | 43.000 to 60.000 | |
3,078 | 108 | 51.000 to 72.000 | |
3,648 | 128 | 60.000 to 90.000 | |
4,104 | 144 | 90.000 to 120.000 |
FILLING TECHNOLOGY |
|||
1. PGF: Mechanical filler with vent tubes and cam control. | |||
2. YDL: Volumetric filler with measuring cylinder for filling volume control with deviation within ±1ml. |
* Add notice about your Privacy Policy here