SXP/XP
Bottle washer for Glass bottle filling line
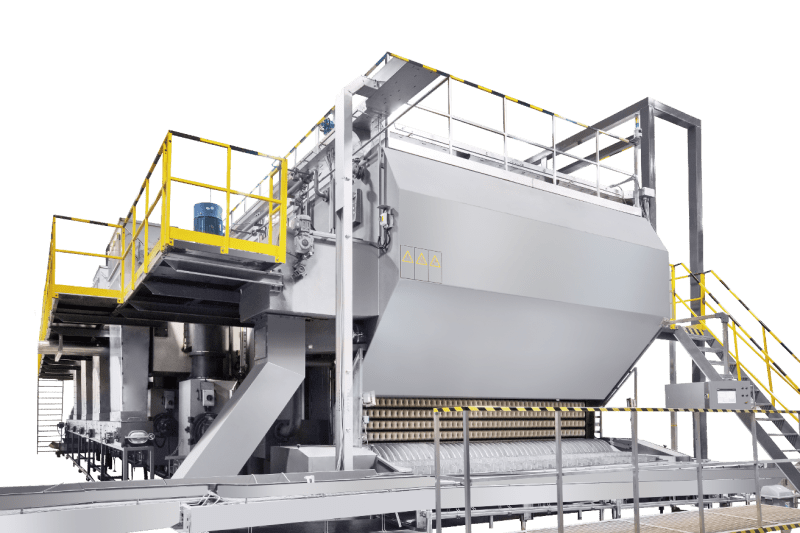
Capacity:
Up to 72.000 bph
Brief Introduction:
- The fully automated bottle washer is used to clean returnable glass bottles according to project requirements and is alternatively delivered in single-end or double-end design.
- Safe and stable loading and unloading of bottles is assured with a reliable gear transmission system with an automatic electronic reset for overload protection.
- The bottles are loaded in full plastic bottle pockets with high acid, alkali, and temperature resistance and are transported gently and efficiently through the caustic bathes of the machine.
- Temperatures and caustic concentrations are automatically controlled.
- The final efficient self-centering/ self-cleaning rotating spraying system guarantees that all caustic residuals are safely removed and the bottles are in full hygienic condition when leaving the washer.
- All washing machines (bottle washers) for Glass bottle components have been selected for energy-efficient operation.
Glass Bottle Washer Machine Benefits: |
|
1. Single-end or double-end execution according to project requirements. | |
2.Hygienic design of discharge section(vapor removal by blowing device). | |
3. Automatic temperature, caustic, and pump control. | |
4. Self-centering and cleaning water spraying system. | |
5. Moisture is kept on the inside and outside of the bottle during the whole washing process to avoid “white bottles”. | |
6. Exhaust system to remove H2 for handling of bottles with aluminum foil. Airflow sensor and machine stop in case of insufficient airflow. | |
7. Reversed conveyors at the infeed table to reduce the pressure in the bottle flow. | |
8. Label squeezing system with a centralized conveyor belt to reduce manual labor. | |
9. Back flush double filters including a monitoring system installed at inlets of spraying pipes to eliminate blockage. | |
10. Online caustic filtration system as an option to remove the paper fiber from the caustic. | |
11. Bottle pockets made from special plastic material to avoid deformation and reduce heat transfer. | |
12. Strong bottle carriers formed by integral stamping without welding with good elasticity, lightweight, and easy to maintain. | |
13. The sealing seat of the spraying shaft is designed with an elastic structure to correct the deformation of the shaft and reduce leakage. | |
SUSTAINABILITY |
|
1. Up to 60% reduced water consumption with individualized settings of pressure and water flow for each SKU. | |
2.30% reduced steam consumption through special plastic material of bottle pockets(less heat carryover) and piping and housing insulation. | |
3.20% power saving by using IE3 or above class motors. | |
4. Fully automated lubrication system for grease dosing with volume and timing control. | |
5.10 years guarantee on all structural parts. |
* Add notice about your Privacy Policy here